常州光圈如何用MR技术帮制造业降本增效?
文/VR陀螺 来福
从2013年德国提出工业4.0开始,全球工业发展进入了利用信息化技术促进产业变革的时代。就国内而言,智能化就是制造业在工业4.0时代的基本转型方向之一。
工业和信息化部部长肖亚庆称,2019年中国制造业增加值占全球比重达28.1%,连续10年保持世界第一制造业大国地位。截至2020年6月,中国制造业重点领域企业关键工序数控化率和数字化研发设计工具普及率分别达到51.1%和71.5%。
随着智能科技设备强势加入制造业,一些一线企业在使用过程中逐渐发现了传统制造业和现代技术的一些矛盾。
其一,现代制造业专用机械功能丰富,但相应带来的问题就是设备维护往往需要专业的对口人才,运营成本水涨船高;其二,整个时代的发展,市场需求由“大而重”转变为“小而美”,定制化的需求旺盛,不管是制造业企业本身还是生产设备提供商,都转变思路向着“即插即用”式产品发展,产品种类相应增多,定制化的设备也随之增多,导致企业管理设备、数据的难度更高。
直指实际生产的矛盾如何解决,是目前很多制造业企业需要面对的问题。
工业后勤为何难上加难?
对于始建于1943年的一汽解放汽车有限公司无锡柴油机厂(以下简称“一汽解放锡柴”)来说,70多年的工作流程面对工业数字化的时代要求,则更加需要攻坚克难。此时,一汽解放锡柴则更需要深挖自身工业生产上的痛点,针对痛点,引进合适的数字科技技术显得尤为重要。
作为为一汽解放锡柴提供MR技术解决方案的常州光圈信息科技有限公司,通过长时间在生产车间、产线的调查发现,后勤是保证高效生产的重要因素,而一汽解放锡柴在后勤设备维护维修上正面临一系列挑战:
1、维修难
一汽解放锡柴主要生产适用于如解放J6等重型卡车或其他大型客车的发动机,普遍的发动机生产、装配都需要上千平米的大型车间,几十台大型机械共同运作完成。在这样承载大机械的空间中,如果某个设备出现问题,需要联系对口的维修人员,在复杂的机械里反复对照图纸、排查问题再进行维修。
而真正执行流程时会发现,一方面,要在故障现场联系到维修人员,需要经历较长的沟通周期;另一方面,维修人员需要从其他地方赶来,这一周期也会浪费很多时间和精力。进而导致一个小问题,需要很长时间才能解决,误工、沟通……无形之中增加了企业的成本。
2、维护难
除了维修之外,维修维护人员团队的维护也存在着问题。
其一,经验要求高。像一汽解放锡柴制造重卡发动机所需要的制造机械,本身结构复杂,需要长时间的接触、了解以及大量的经验累积才能快速精准的解决问题,这就导致了企业更愿意用老人,而很难启用新人的人工分配不均问题。
其二,人员流动大。制造业企业工作环境和节奏比较艰苦,维修人员需要大量的出差,但对一些年轻人来说,收益不如互联网企业,会产生频繁的离职再招人现象,导致企业刚刚培训的人,转眼就回到了人才市场。 由此,企业的维修维护团队就面临着“老人不够用,新人招不上来”的尴尬处境。
3、可持续难
数字化转型另一个特征就是将企业原本的知识性生产资料、人才库转变为数字存档、内部共享。而目前不仅仅是一汽解放锡柴,大部分传统工业企业都仍旧保持着知识、经验、数据等生产资料的“人传人”的分享方式,尚未完整建立起成熟可用的内部数据库,导致人才培养、设备维护等无法进入可持续循环发展状态。
通过总结分析调研结果,常州光圈将技术方案落地点聚焦于一汽解放锡柴的设备维修维护上。在VR陀螺的采访中,常州光圈总经理黄敏明说:“我们逻辑就是,现在维修工作繁琐、人员培训困难、技术水平有待提升、团队很难维持,此时引入MR技术,把数据和流程的问题解决了,就是一个很好的解决方案。”
MR优化作业流程修不难,学也不难
黄敏明所说的解决方案就是常州光圈历时近一年,为一汽解放锡柴的设备维修维护量身定制的“一汽锡柴MR培训及维护支持软件系统”,该项目一期目前已经在一汽解放锡柴落地实施。
简单来说,一汽锡柴MR培训及维护支持软件系统是通过HoloLens 2将2D/3D影像精准投射在实际环境的某个位置上,把以往复杂的信息转换为视觉表现,同时通过简化、教授维修操作,降低其上手难度和要求,充分提高了维修效率。
据了解,之所以说是为一汽解放锡柴“量身定制”,是因为“一汽锡柴MR培训及维护支持软件系统”是完全有针对性的解决目前一汽解放锡柴维修维护上遇到的实际问题。 首先,常州光圈通过与连接一汽解放锡柴的设备、工程师到场实地测量等方式,建立了定制的数据库。
“遇到问题时,系统读取设备的状态参数,根据状态参数做出故障判断或问题状态判断。如果问题比较简单,就直接调用知识库指导解决。目前这种自动化的程度大概是60%-70%,而且仍然在提高。”黄敏明说。
其次,常州光圈利用MR技术为一汽解放锡柴的维修流程优化。作为70多年的老牌工业企业,一汽解放锡柴拥有完整、熟练且高效的工作流程,很难彻底改动,改动的成本也很高。而常州光圈则是选择在原有的维修流程上进行优化,把负面影响充分降低。
前文提到,原本的维修流程中,等待经验丰富的维修人员到场的时间成本很高。在常州光圈的方案中,把问题的判定和一部分维修工作交给了AI和戴着HoloLens 2的操作员。设备遇到问题,由AI介入判定问题,再由操作员选择是否进行微信或呼叫专业维修人员。
“比如说,现场遇到A错误需要打开某个盖子解决。通过传输回来的数据,戴着AR眼镜的操作员可以看到一个动画,告诉他应该打开某个盖子,操作员只需要照着做就可以了。”黄敏明描述道。
“但目前还会有一些问题需要人工综合判断,这时候可以调用远程支持。通过MR共享画面,远端的工程师、专业维修人员可以指导操作员操作。当然,虽然说这套系统极大程度降低了人力成本,但我们也承认有一部分问题必须工程师或者专业维修人员亲自到场,这时候再联系就可以了。” 根据黄敏明的描述,通过MR共享画面,工程师、专业维修人员直面现场的时间是原来的1/10甚至1/20,免去了大量等待的时间。
而以上的高效便捷都是建立在第三点:人才培训系统和数字知识库上的,也是帮助企业数字可持续的重要关节。
黄敏明说:“现在他们的维修数据、维修知识库很多还是口口相传,或者以视频的形式存档,我们要建立知识库,就是用动画、建模把它这些知识和流程做出来。” 据了解,目前项目一期已经完成,针对性的知识库也已经建立。黄敏明表示,在未来的二期、三期中,会逐步完善,并构建一个编辑平台,由企业自行导入、建立知识库。
通过硬件方面利用HoloLens 2,软件方面对原有流程的优化、建立维修数据库、人才培养平台等,常州光圈帮助一汽解放锡柴搭建的“一汽锡柴MR培训及维护支持软件系统”,可以说是逐步的解决了一汽解放锡柴目前维修上遇到的困境,节省了大量的人力成本,并帮助其迈向了维修可持续化发展。
实践出真知,时间和人力是MR B端落地的真正壁垒
在实际落地过程中,直面生产车间,与一线人员进行沟通,常州光圈有了非常多的体会。
在项目初期,就面临着选择什么样的硬件平台做研发,最终常州光圈选择了HoloLens 2。对于这样的选择,黄敏明说:“主要基于三个方面,第一,硬件设备的基础性能,我们想要前端人员真正使用它,这一点就很重要。拿FOV举例,车间很大,如果FOV太小,工作人员要同时看两台设备的数字信息怎么办?还有投射精度。我们需要用起来,数字标注到投射到准确的位置很重要,出现偏差的话我们做的东西就没意义。”
“第二,交互。HoloLens 2的手势识别精度和准确度足够高,能够大大减少我们推行这套系统的阻力。”
“第三,软件。微软是大企业,我们使用HoloLens 2硬件的同时也获得大量的基础软件服务。很多基础的工作,比如空间定位功能,就不需要我们单独开发。包括后期,随着数据量增加,我们也会用到微软的云渲染服务。也可以说借用微软的平台,我们有了一个比较简单的技术壁垒。”
接下来真正推行项目时,常州光圈也遇到了只有在实际执行中才会遇到的细节问题。比如面向的企业数字化程度不高,黄敏明对此深有感触:“数字化程度不高,我们正在推行的1.5期里,就有很典型的例子。”
“1.5期我们的应用对象是换刀车床,有一个电柜样的操纵板。图纸是德国企业提供的,他们只做了很简单的标注,比如第一排、第二排、第三排分别是A、B、C类,但具体接入什么线路、什么东西,图纸上没有。我们接触到的工程师也不是原厂工程师,如果只看图纸,在实际维修中提供不了帮助。”
“他们的解决方法是贴标签,对于工作十几年、有经验的工程师来说,这当然没问题。如果新来一个工程师,就需要他一次次去反复看标签,显然很费时费力。我们一部分工作就是在图纸模型的基础上做调整。”
“而一期面向的这台设备,受限于场地,他们就把原本标准模型的3米长,改成了2.8米长。这种信息,你只是靠看图纸肯定是不行的。所以要搭建数字化管理平台,这个工作很繁琐,一定需要人到现场去。”
在从想法到实际落地再到一期完成,顺利的背后是常州光圈处理了许许多多类似“实际设备不对版”的问题。黄敏明表示,本月就会开始1.5期项目的持续推进。
“1.5期就指的是我们要把目前这套解决方案,移植适配到另外两台设备上。后面会继续跟进二期,在工厂内部继续推广,让我们的方案在锡柴内部跑起来,需要增加硬件、系统的数据等等。三期目前也是有规划的,就是争取推广到一汽集团。”
关于为什么要做对工业企业的MR项目,黄敏明说:“因为看好未来的市场。就目前的情况来讲,需求是明确的,像三一重工、中联重科、特斯拉等制造业企业存在需求,另外还有一些纺织业等轻工业也都表示愿意尝试。所以需求是存在的,但问题在没有人实际的跑起来。”
“没人愿意跑起来去做”也反应在项目实际落地的过程中。黄敏明和其团队发现,由于可用于工业的AR眼镜选择很少,所以各个团队之间真正的技术壁垒并不明显。 最明显的壁垒其实时间和人力,也就是在项目实施中,实际数据和图纸数据不匹配,需要常州光圈的工程师长时间驻扎在工厂进行调研、测量才能导入并进行数字化管理。
“我们的工程师将近一半的工作时间都在厂子里度过。”黄敏明说。
对于常州光圈来说,将MR技术真正带给一线工作人员,所需要付出的是在建模、实地考察、反复沟通磨合上的成本,但也带来了巨大的收获。黄敏明说:“争取在明年三季度开始二期,同时我们也会继续接触像三一重工这样的企业,把我们的技术投入到更多一线制造业的使用中去。”
此外,黄敏明还谈到了在与传统企业合作时的心得:“第一,推行项目的时候要让对方有意愿。传统企业每一个都有它的运转逻辑,你要想撬动它某个点,就得让他们产生意愿,才能顺利高效的沟通;第二,我们自身要有很高的能动性。因为B端有B端的逻辑,产品必须要产生实际价值。再比如一些制造业企业愿不愿意用MR,你不去问不去跑,是得不到信息的。有些想法也是,只有实际看了才知道能不能用,有没有效果。”
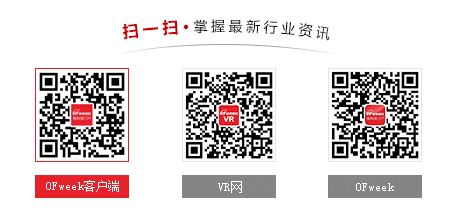
最新活动更多
-
7.30-8.1火热报名中>> 全数会2025(第六届)机器人及智能工厂展
-
精彩回顾立即查看>> 【线下论坛】新唐科技2025新品发布会
-
精彩回顾立即查看>> 【在线直播】解密行业检测流量密码——电子与半导体行业
-
精彩回顾立即查看>> 【深圳 IEAE】2025 消费新场景创新与实践论坛
-
精彩回顾立即查看>> 【限时免费】安森美:Treo 平台带来出色的精密模拟
-
精彩回顾立即查看>> 【在线会议】ImSym 开启全流程成像仿真时代
推荐专题
发表评论
请输入评论内容...
请输入评论/评论长度6~500个字
暂无评论
暂无评论